As farmers across the Midwest prepare for the busy fall harvest and tillage season, we have a very simple yet vital message for you: Remember your tires and rims as you prepare your equipment for your busiest time of the year. A cracked rim, loose lug nuts, or sidewall cut can bring your harvest to a halt. And we can almost guarantee that the failure won’t happen at a time or place that’s convenient to you. Plus, there’s the safety angle: You want to be sure you and your workers are safe while working your land. This involves both training and well-maintained equipment. We created the following checklist to help you roll smoothly through harvest.

7-Point Tire & Wheel Inspection Checklist
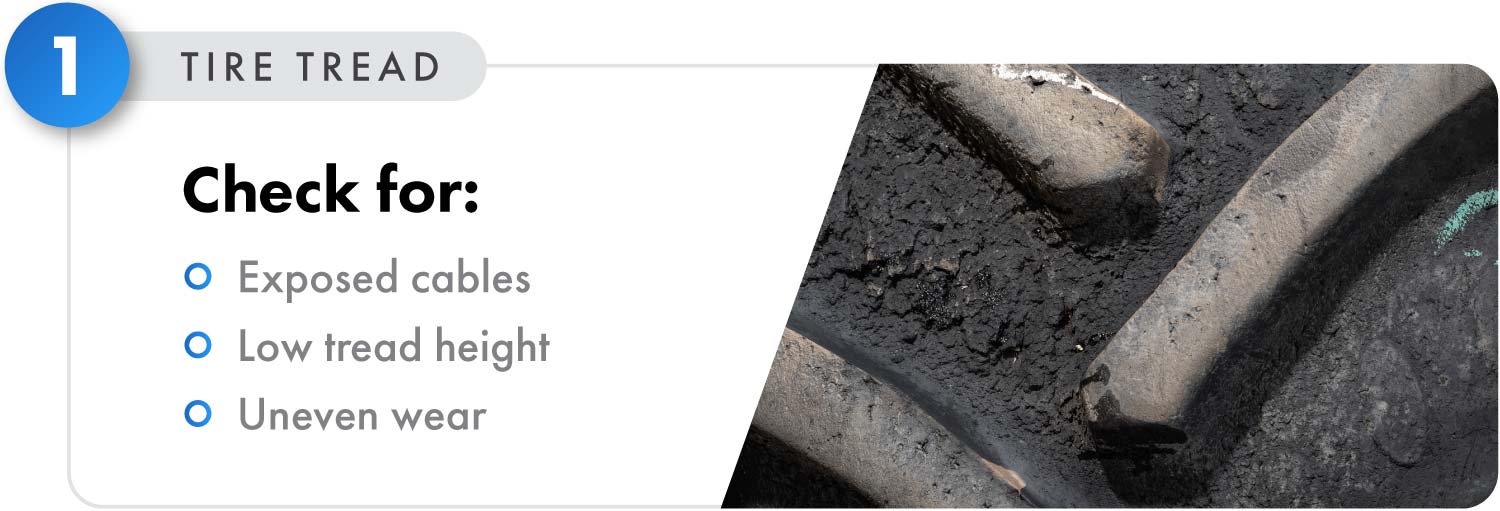
1. Tire Tread: Healthy Tread Saves Fuel and Time
- Stubble/Hazard Damage: Field hazards such as stubble and rocks can cause chips and cuts along the tread bars (called erosion). You can roll with minor wear. But if your tread bars are significantly worn, with fabric and or cables exposed between the bars or deep cuts or large chips, it’s time to replace the tire.
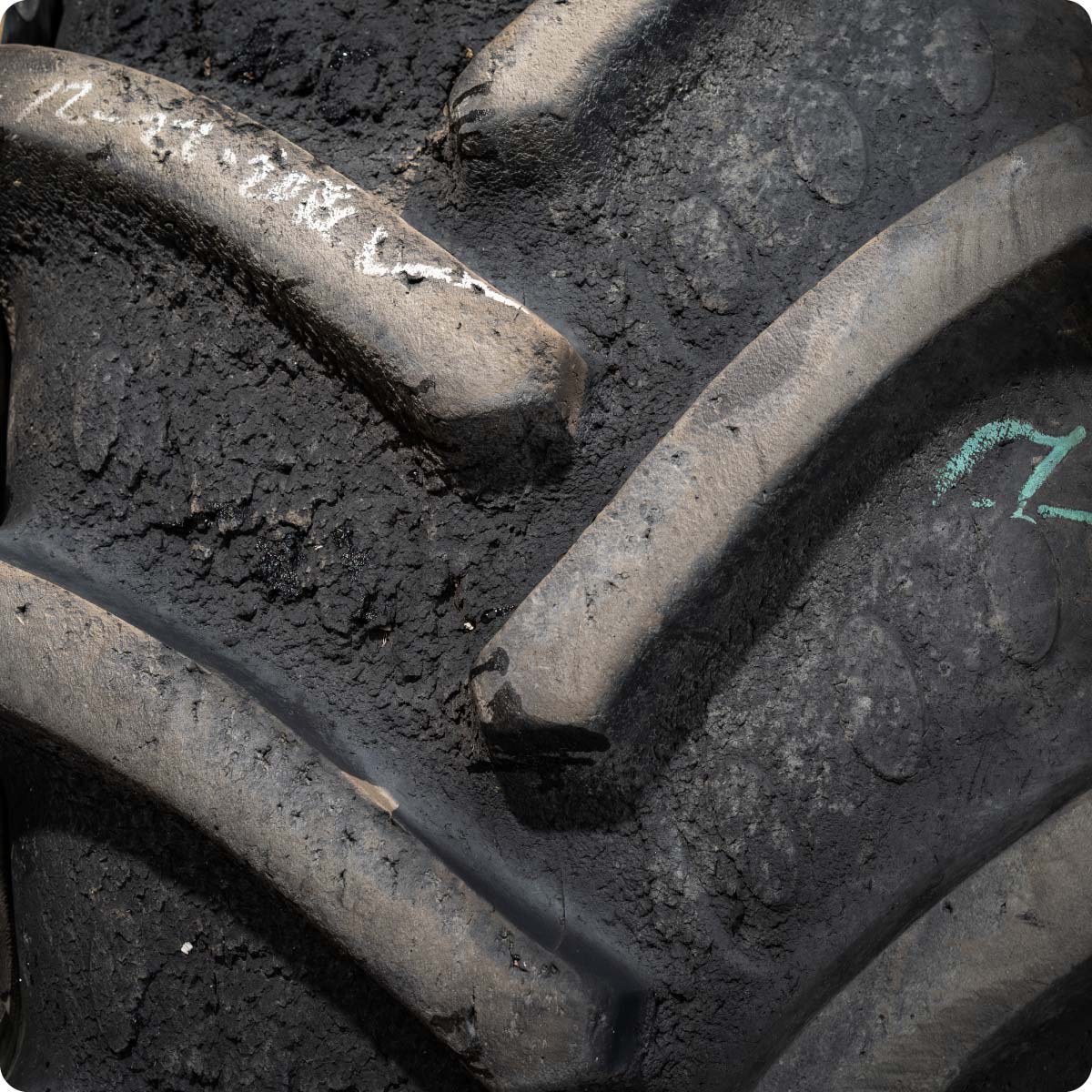
- Tread Height: Tread less than 20% of its original depth warrants replacing a tire. As you lose tread depth you increase slippage and decrease traction. This will inflate your fuel bill as engine RPMs are wasted on slipping instead of moving you forward.
- Uneven Tread Wear: Does your tire tread look like a flat-top haircut or the opposite? You may have over- or under-inflated tires. If you see other signs of odd wear you may have an alignment problem. If the odd wear is too severe, you’ll lose traction, which will lead to a longer, more expensive harvest.
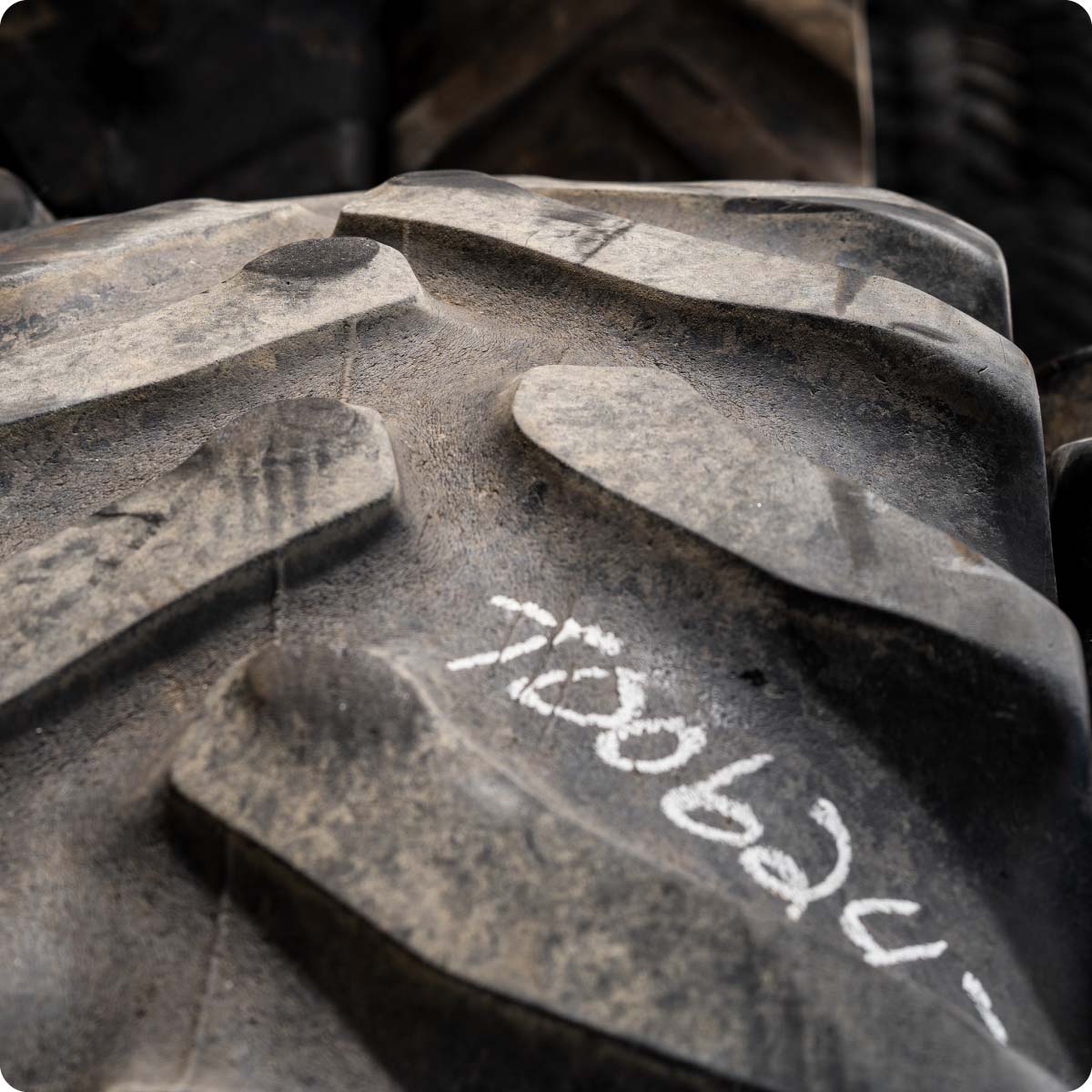
Are you running worn tires but don’t have a new set in your budget for 2021? You can work with NTS Tire Supply to find a set of quality used tires to carry you through the fall and beyond.

2. Sidewalls: Don’t Let Tire Damage Stall Your Harvest
Look for cuts, tears and bulges in your tire sidewalls. A bulge can indicate internal tire damage—maybe from striking a rock or a tree stump. A bulging tire is not repairable and you’ll need to replace it. If you see fabric through a cut or if the cut is close to the bead or shoulder of the tire, you’ll want to replace it as well. These won’t go away and may cause a tire to fail. Older tires, even if they don’t have a lot of hours on them, can fall victim to dry rot—a condition that stems from exposure to dry air and sunshine. If your tires look faded and dry and are crossed by numerous small hairline cracks, you might want to consider replacing them.
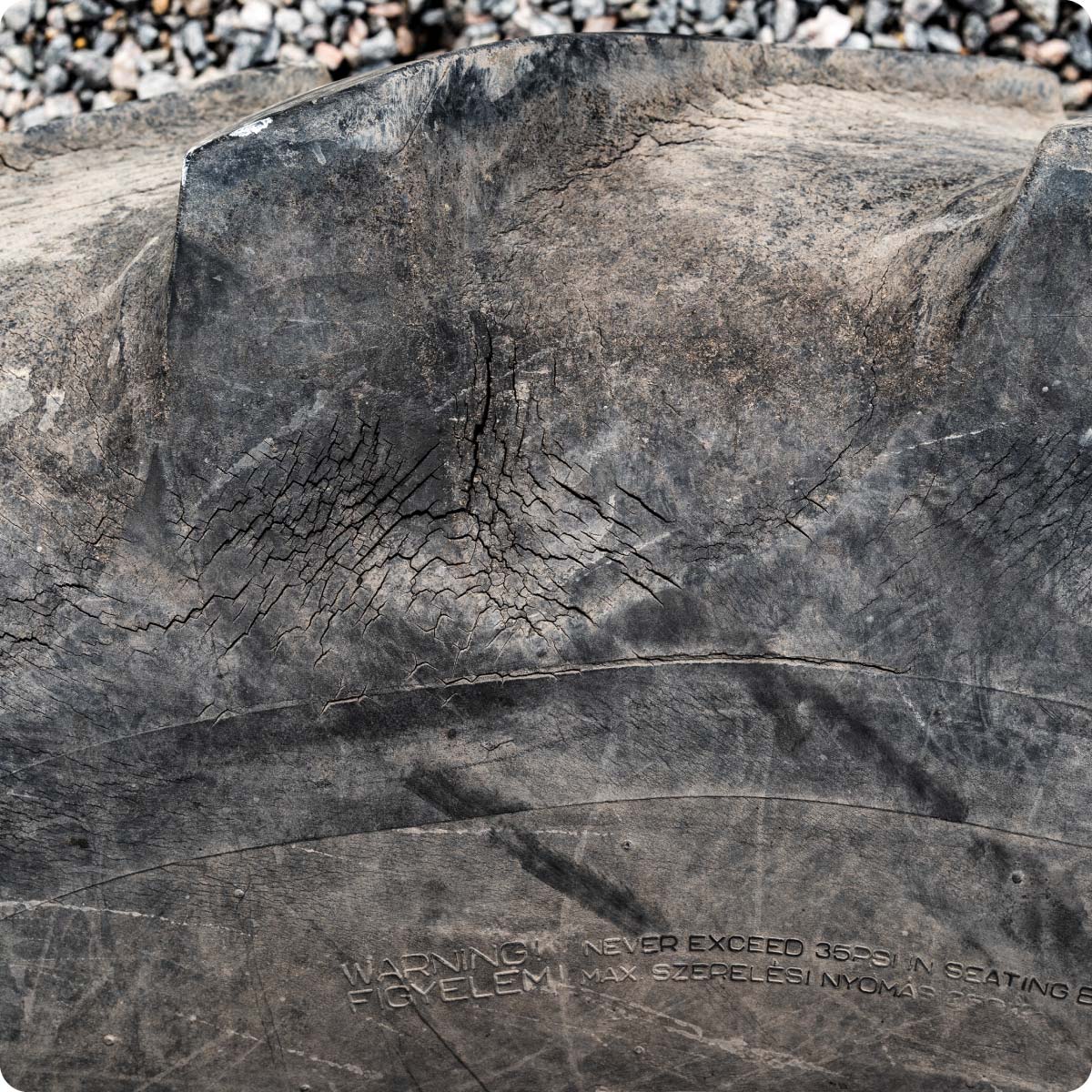
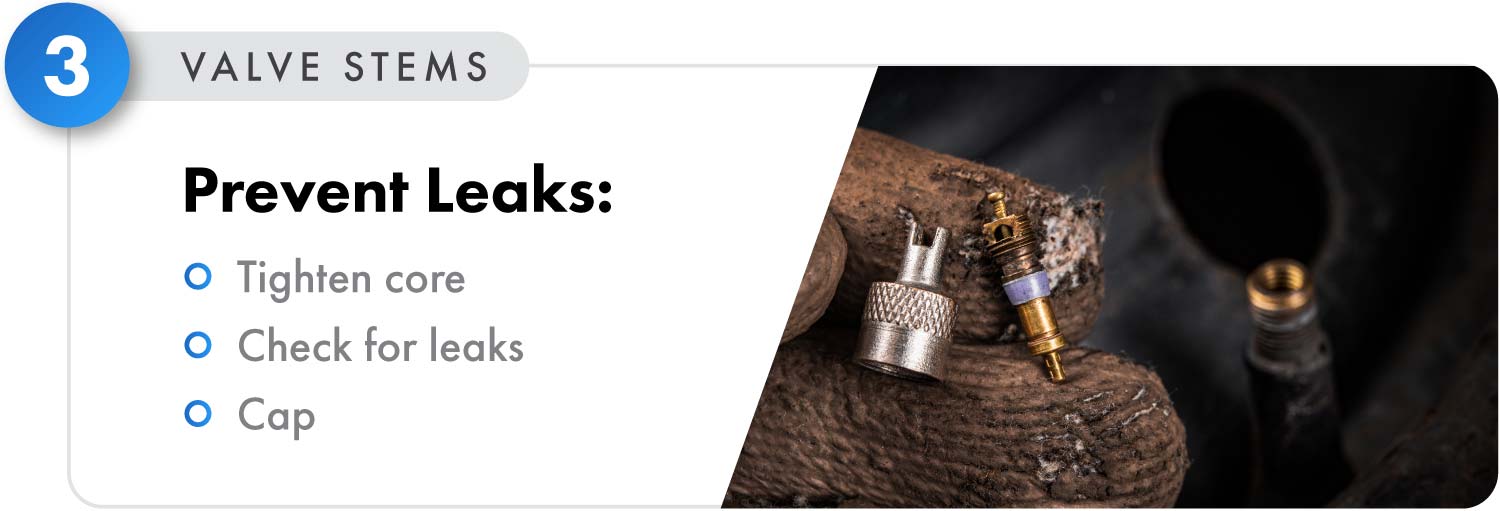
3. Valve Stems: Even a Small Part Can Cause a Big Leak
If you’re always airing up a tire, your valve stem may be the culprit. Check to be sure the valve core is tight and that the stems aren’t loose or showing signs of dry rot. And be sure to cap your valve stems so you’re not having to dig mud or debris out of a stem with a jackknife before you can air up.
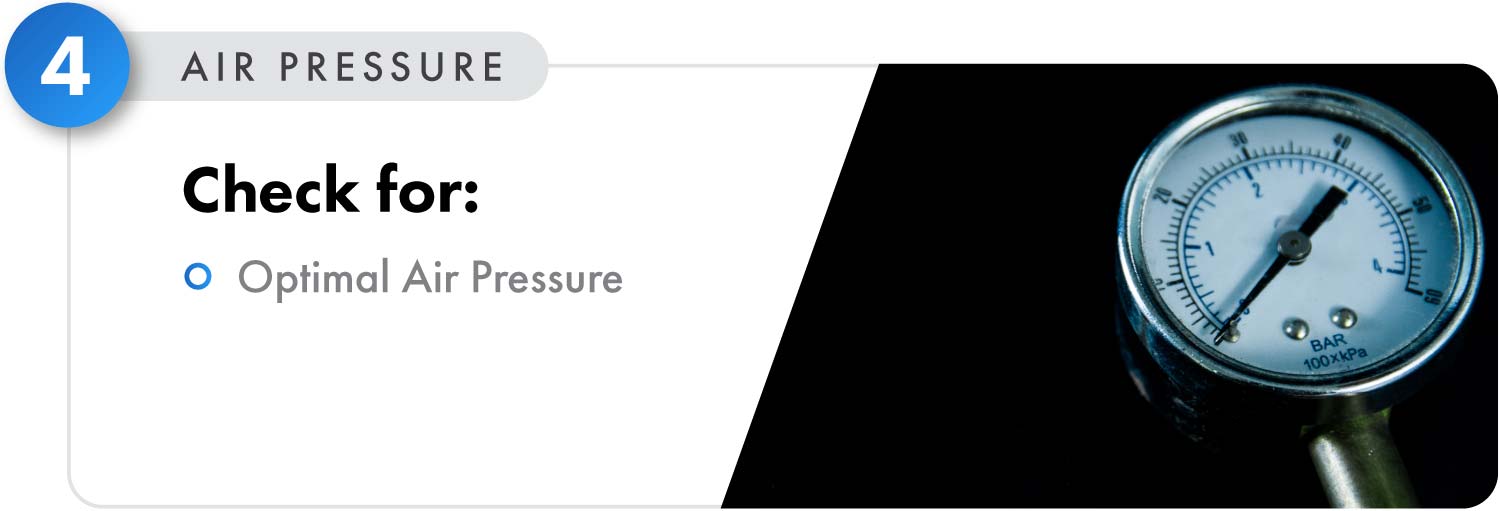
4. Correct Air Pressure: Essential for Top Performance and Longer Tire Life
To get top performance from your tires and avoid excessive wear you need to run them at the correct air pressure for your machine’s weight and application. This is where your owner’s manual or loading information from your tire manufacturer’s website is vital. With today’s high tech tires, it’s especially important to set your tire pressure for specific conditions and implements. Operating your 4WD with 7 psi in the field may be ideal, but running several miles down the road at that same 7 psi may ruin your tires. If you’ve invested thousands of dollars in premium ag tires, you may want to consider a central tire inflation system (CTIS).
Read More: Transform your tractor into a lugging beast with a central tire inflation system.
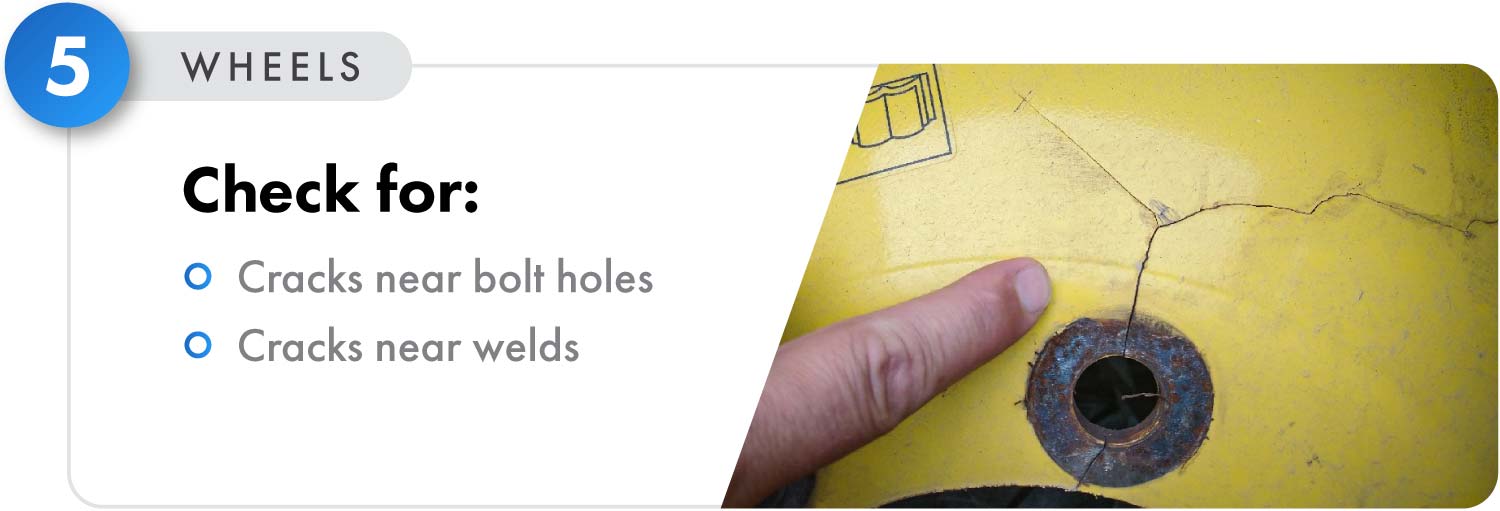
5. Wheels: Watch for Cracks to Avoid Downtime
Take the time to properly inspect your wheels—especially combine wheels. Go slow and be sure to methodically check all areas of the wheel surface. Use a bright light to make it easier to discover small cracks. We receive numerous calls every harvest season for emergency repairs due to wheel failures. Cracks start small and can quickly grow catastrophic when you subject the wheel to pulling forces and/or a heavy load. See rust or dark-looking streaks originating from under the lug nuts? Cracks at the outer edges, on the face, or between the lug nuts? Address the failing wheel now, or you might be faced to confront it during harvest.
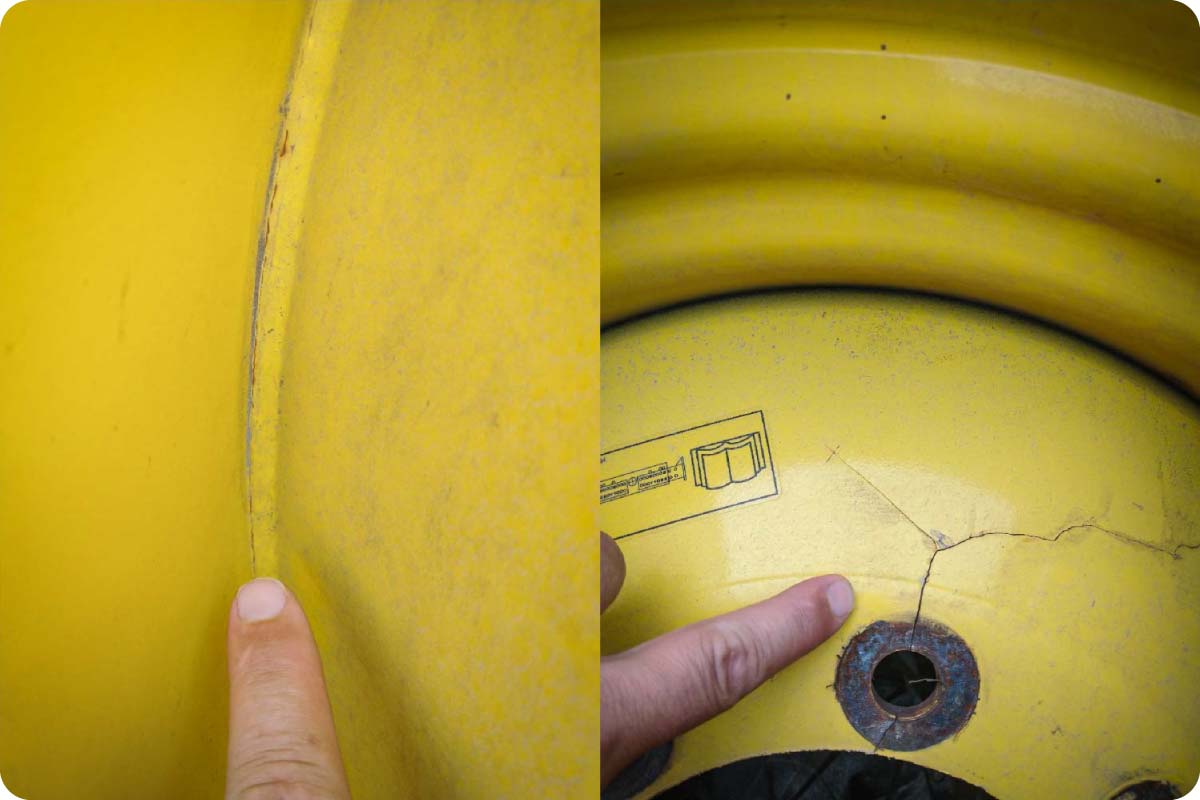
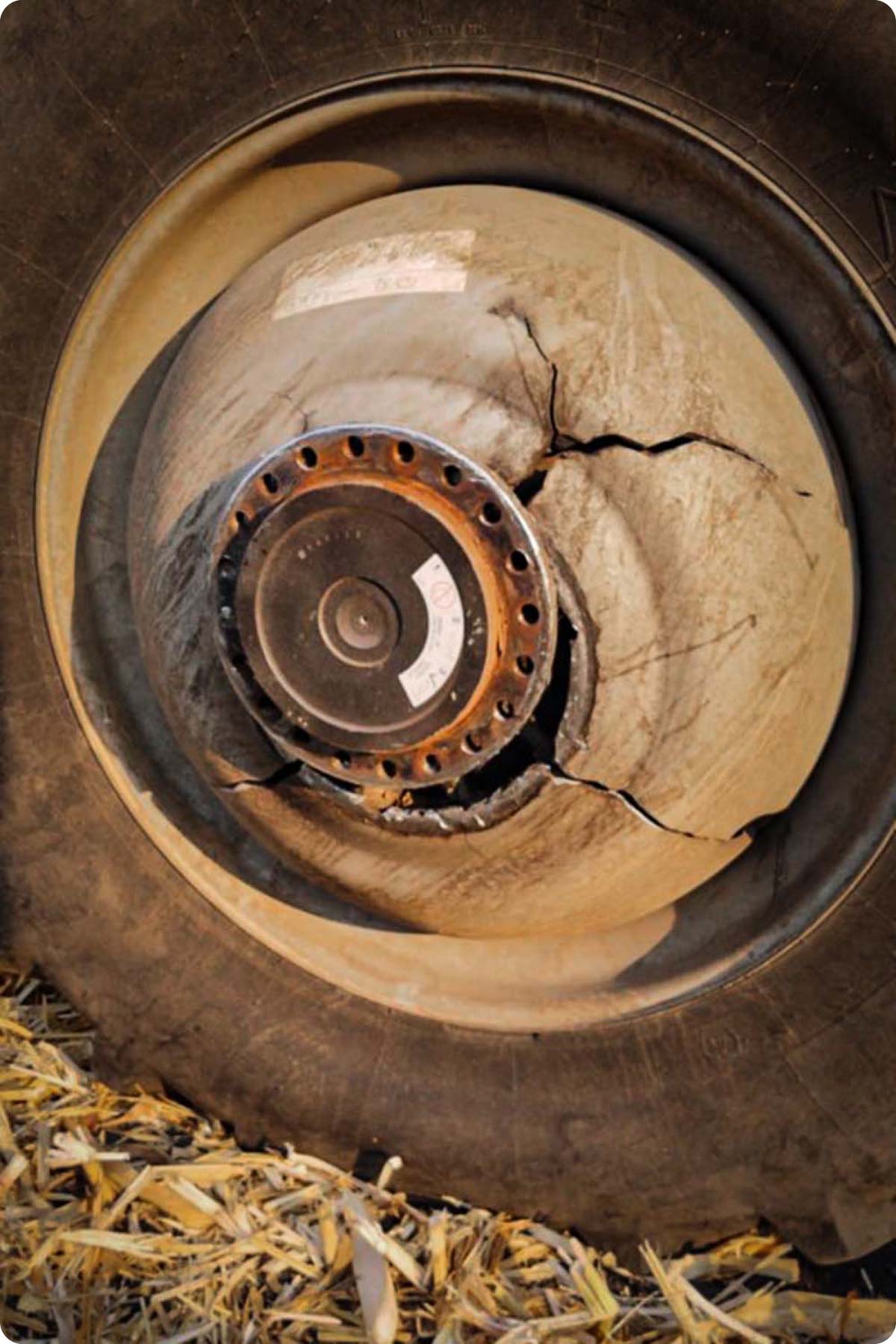
Is it Wise to Weld a Cracked Wheel?
At NTS Tire Supply, we don’t recommend weld repairs on wheels. (The only exception would be to cut out the entire center and replace it.) Why? We’ve seen it again and again: someone welds over cracks on their wheels only to have it crack again right beside the weld repair. No one really wants to shell out a bunch of money for a new wheel, but even with a weld repair, you’re still going to have to replace the wheel eventually. Generally, you’ll spend more money in the long run to limp along on a welded rim.
You can weld a reinforcement ring around the lug holes, but you should have this done before cracks start. Once a rim has started to crack, it really isn’t safe to continue using it.
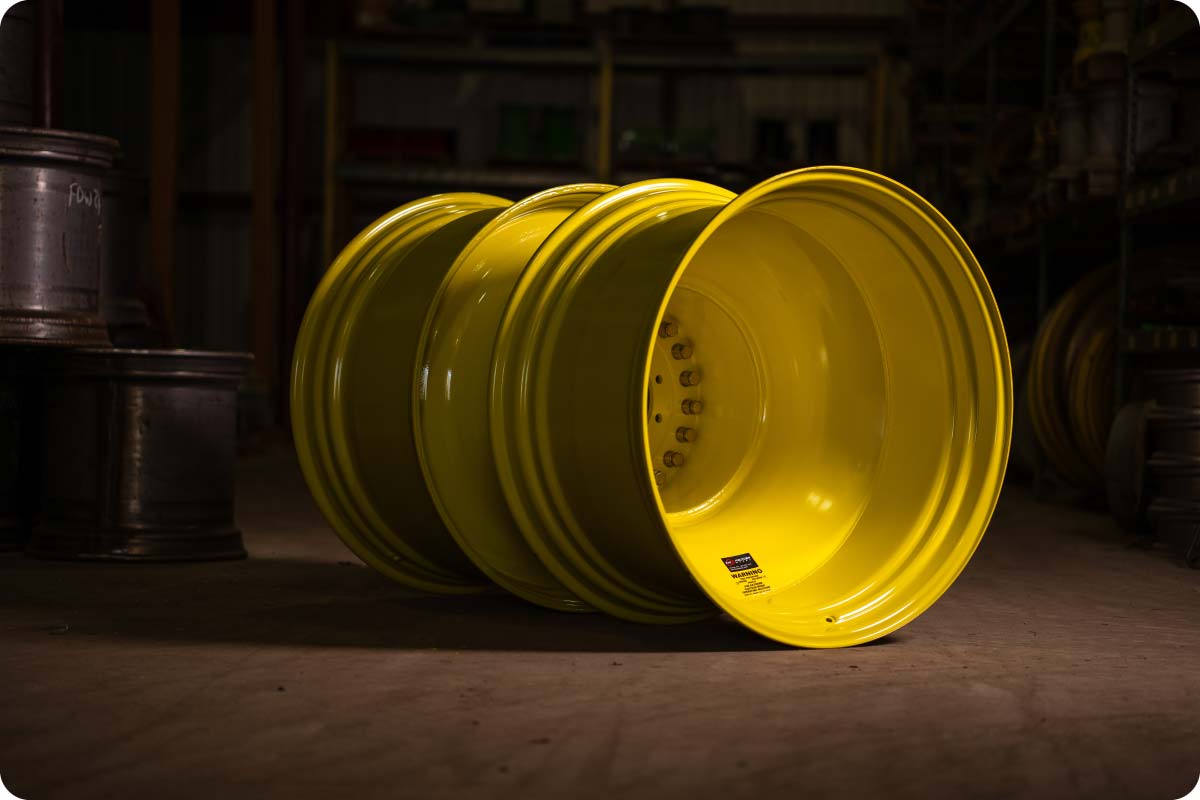
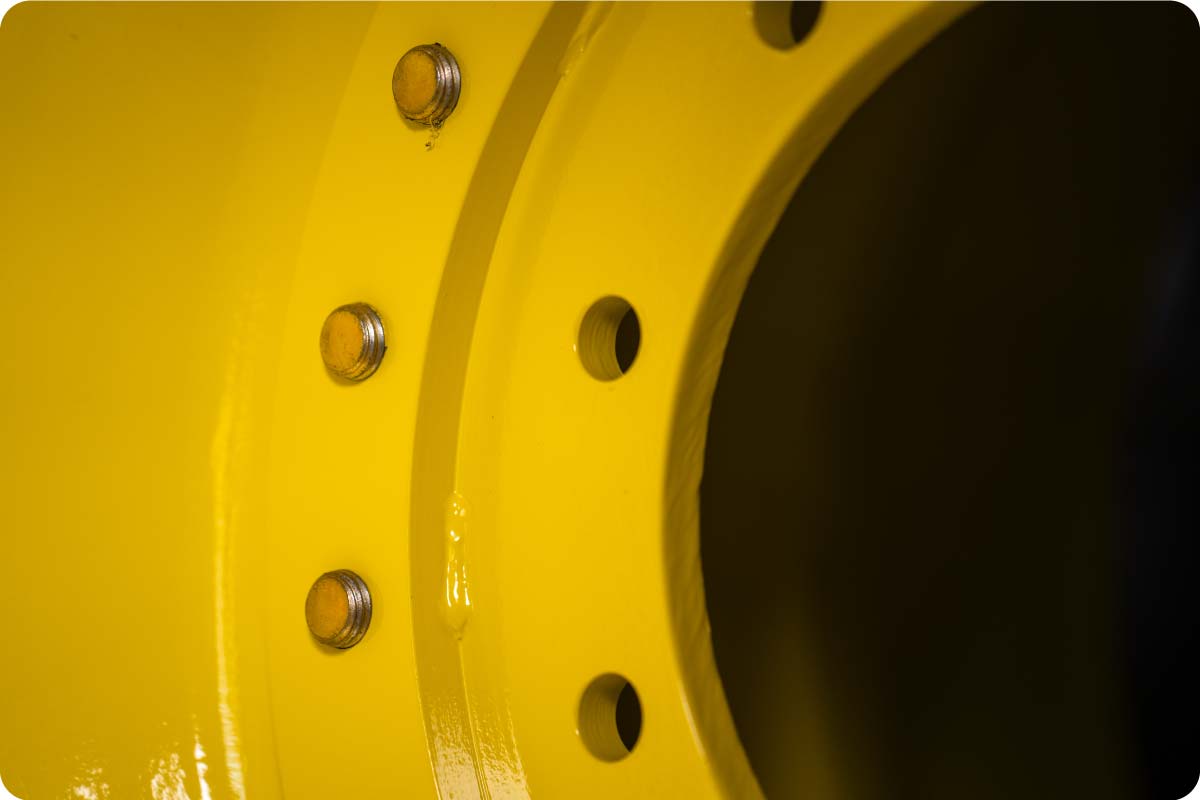
Fix Cracked Wheels Permanently: Upgrade to HD Straddle Duals
There are stronger wheel options out there for combines, including our very own HD version of straddle duals, which are designed for class 9 and larger combines. They are built specifically for today's heaviest combines:
- 20% thicker steel on main wheel over O.E.
- A one-piece spun flange and tube eliminates welds that commonly fail on regular duals.
- More holding power with larger diameter tube/flange and 0.75" thicker threaded ring (on 20-hole wheels).
- Bead flange reinforcements on main wheel.
- Durable powder coat finish.
If you’re interested in protecting your harvest uptime and want to roll with wheels that will withstand fall’s toughest conditions for seasons to come, invest in a set of our HD straddle duals.
Read More: Increase harvest uptime with HD straddle duals.
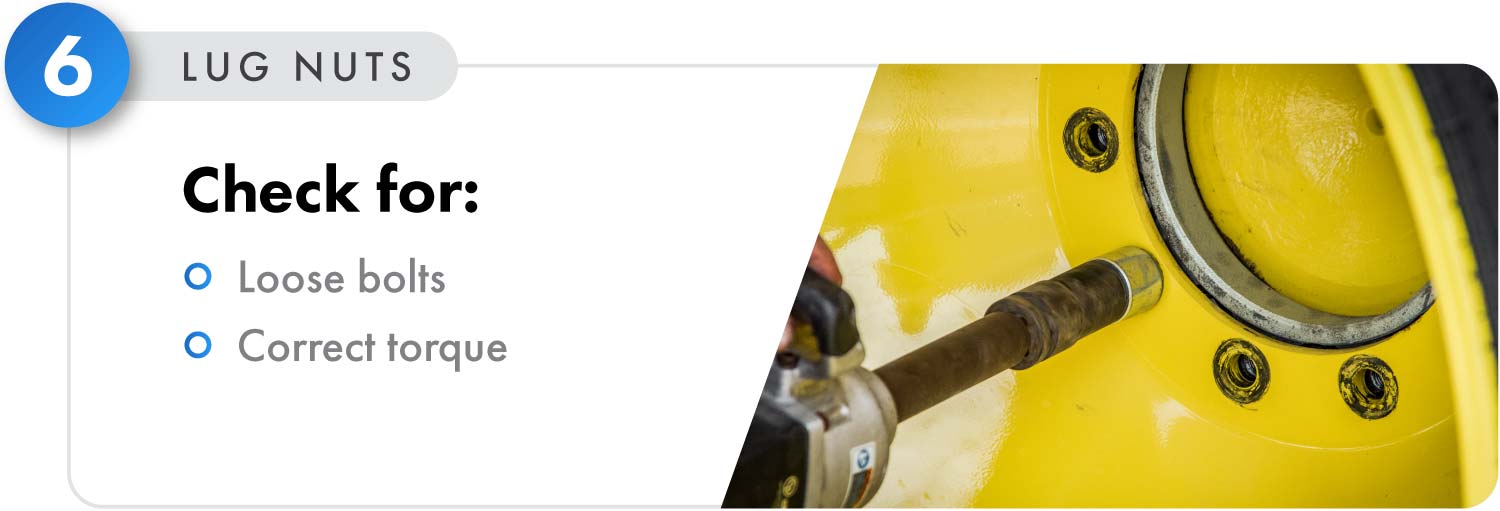
6. Lug Nuts: Critical to Keep You Safe & Harvest Moving
It’s time to dig out that owner’s manual again. It’s important to regularly check the tightness of your machine’s lug nuts. This not only prevents a wheel from separating during operation, it also helps maintain a secure bond (the correct clamp load) between your rim and hub to reduce wear.
Overtightening can stretch lug studs and cause them to fail or “pancake” the metal behind the lug bolt, which can contribute to forming cracks. Under tightening can cause friction between the wheel components, which leads to failure too. Find the right torque for your lug nuts in your owner’s manual—don’t assume it’s the same for all your equipment.
Check nut torque before the busy season and periodically during heavy use. Use a torque wrench to achieve the correct tightness: using a large impact usually leads to overtightening, especially if you’ve applied grease or other lube to the threads before mounting the wheels. When mounting duals (or rims in general), the surface should be clean and free of debris. A dirty surface can lead to under tightening and increased friction.
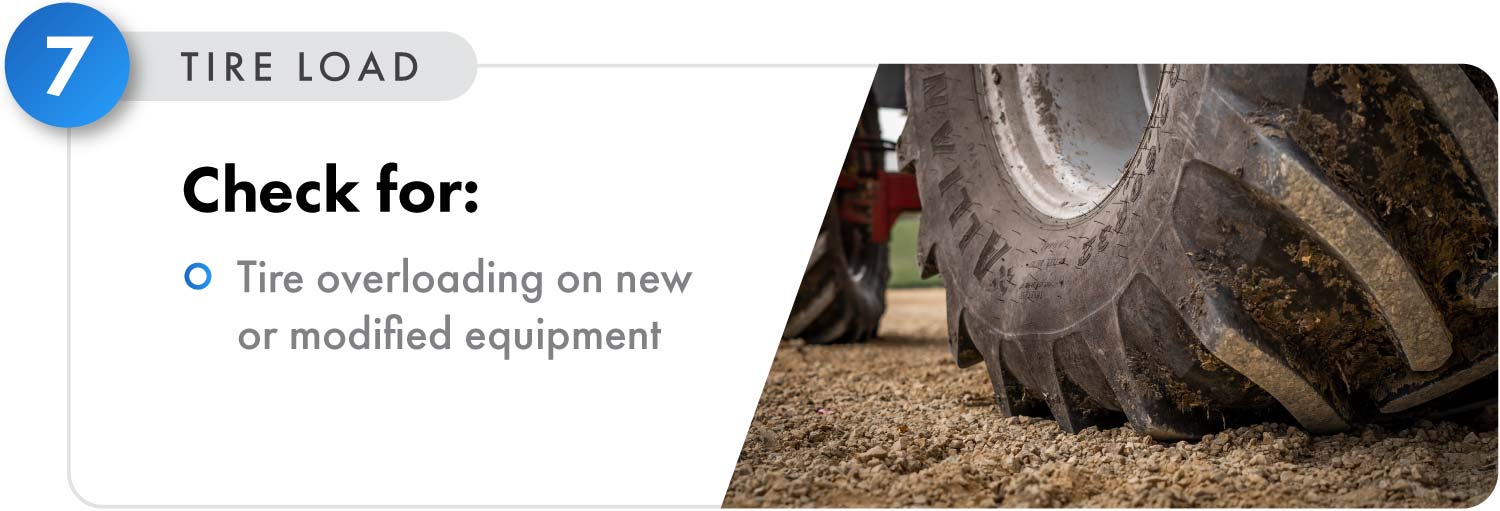
7. Tire Loading: Know Your Limits to Prevent a Failure
Have you upgraded to a bigger grain cart? Extended the hopper on your combine? Purchased a larger ripper to finish tillage earlier? You may want to consult your tire manufacturer’s website—or call NTS Tire Supply—to be sure your current tires are up to the increased demands you’re about to place on them. Any time you purchase a larger implement is a great time to review your farm’s traction plan; you never want to exceed the maximum tire/wheel load. One of our tire experts can review your setup to see if you need to adjust your pressures or upgrade to a new set of tires to handle the load.
Need new rubber? Now is the time to avoid tire failure and gain a performance advantage.
Talk to an expert at NTS Tire Supply to learn if you’d be money ahead to invest in the latest generation of tire technology rather than squeak by with your old rubber this fall. As long as you have to replace a worn-out or damaged tire, it may be smart to invest in the latest generation of ag tires that can boost traction and fuel efficiency and reduce compaction across your fields.
Carry More Weight at Lower Inflation Pressures with CFO (Cyclic Field Operation) Tires
Despite the jargon, these tires bring a straightforward benefit to your combine or grain cart: the ability to safely carry more weight across your fields for short periods of time. They’re designed to run “overloaded” in situations where a machine’s weight varies from minute to minute during normal operation. Hopper full . . . hopper empty . . . hopper full. You get the picture.
Get More Tread on the Ground with IF (Increased Flexion) and VF (Very High Flexion) Tires
Michelin first brought IF tires to the marketplace in the early 2000s, and now all the major manufacturers offer IF and VF tires in their product lines. IF tires can carry (up to) 20% more load at a standard radial’s inflation pressure. Or they can carry the same load (as a standard radial) at 20% less inflation pressure. The story’s the same with VF tires, only increased to 40%.
If you’ve purchased larger, heavier equipment or want to fight compaction or gain efficiency through better traction this fall, an IF or VF tire upgrade might be right for your operation. As a bonus, the stout, highly engineered sidewalls on these tires are better at resisting stubble and other hazard damage. And their larger footprints deliver more traction while saving your fields from excessive deep-soil compaction, which can occur with inferior rubber.
If the need for new tires or wheels crops up during your pre-harvest checks, be sure to call or drop NTS Tire Supply a line. A traction expert will ask you about your operation and find the best balance of price and performance for your needs. And if it’s a used tire or new hardware that’s in order, we’re ready to help with those needs too. Be sure to take time this summer to review the tire and wheel health on all your equipment and hopefully a tire or wheel failure won’t slow your harvest down.